This website uses cookies so that we can provide you with the best user experience possible. Cookie information is stored in your browser and performs functions such as recognising you when you return to our website and helping our team to understand which sections of the website you find most interesting and useful.
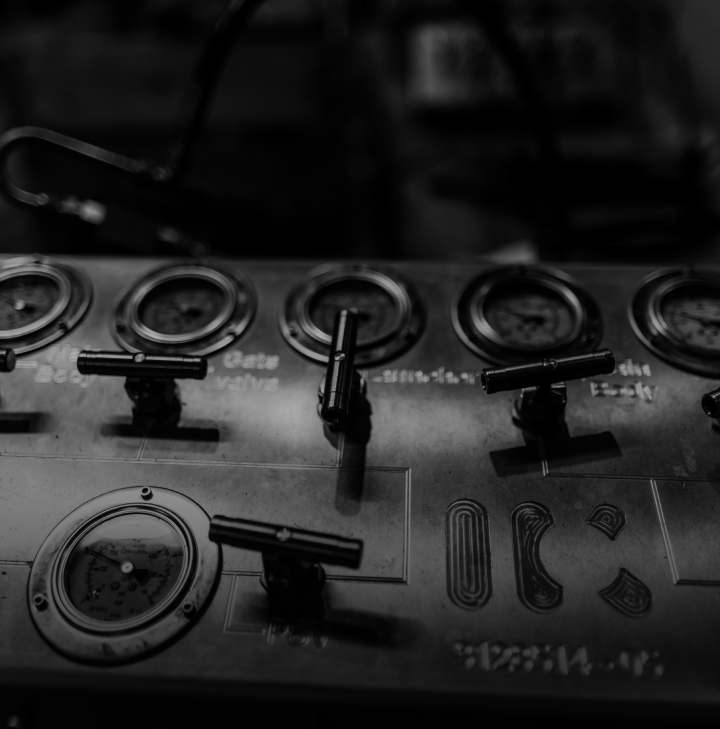
Simple. Safe. Smart.
AOGV
Mechanical
isolation hero
Postponement of planned shutdowns and required maintenance
increases the risk of unwanted incidents and longer shutdowns
down the road. Now there is a solution that doesn’t require
shutdowns!
Isolation without shutdown
The patented AOGV mechanical isolation system installs a barrier between a flange pair on a pressurized system whilst in continuous operation. Unlike alternative isolation technologies, the AOGV allows our customers to safely isolate process segments for inspection, maintenance, or repair without a cashflow shutdown!
“Microsurgery”
With the AOGV you put the isolation points closer to the problem. By reducing the impacted work area, you reduce maintenance time as well as the need for drainage, venting, purging, and flushing. You even reduce your carbon footprint!
No permanent impact
The AOGV provides positive isolation without any physical modifications or lasting impact to the process plant. Once the operation is complete, the flange pair is returned to its original state with a new gasket, bolts, and nuts. The AOGV mechanical isolation system removes the need for costly and time consuming redesigns, new plant certification or new facility drawings.
AOGV application versatility
Repair and modifications
of parts of process
facilities
Retrospective
installation of equipment
Installation, repair, or
replacement of valves
Emergency plant
and piping repairs
AOGV = pure OPEX sense
According to our experience each AOGV application represents a saving of 2 to 20 MUSD-
mainly due to increased production uptime! Moreover, the AOGV adds flexibility to your
maintenance strategy, and it can provide certified lifetime extension for your process plant,
refinery, or oil & gas installation.
The AOGV provides positive isolation without any physical
AOGV Fleet
The AOGV – Add on Gate Value, is a field proven patented technology which
inserts an isolation spade on a live flanged connection thereby reducing down
time and eliminating the need for extensive isolation activities
Size
CL150
CL300
CL600-CL1500
Check points for choosing AOGV
The AOGV provides positive isolation without any physical modifications or
lasting impact to the process plant.
Positive isolation
AOGV is the most secure method
for energy isolation. It facilitates
both spool removal (“air gapping”)
as well as blind isolation.
Pressure monitoring
The pressure within the AOGV is
monitored and safeguarded
throughout the job. Should an
unsafe situation arise, work can be
stopped at any point.
Reduce risk
Unlike temporary isolation plugs, with the AOGV there is no risk of plugs blowing out.
The AOGV also covers a wide range of materials including at cryogenic temperatures where conventional freeze plugs are less robust
Track record
The AOGV has been successfully used
in the field in sizes from 1” up to 36” and
on pressurized hydrocarbon systems up
to 2,175 psi. Workshop testing has
verified operation at temperature
ranges from -261 F to +392 F.
FAQ
At what temperature and pressure can the AOGV be used?
- Temperature range: – 280°F to + 400°F (-173°C to +200°C)
- Pressure range: up to 2500 psi (175 bar)
For which sizes of pipes and pressure class combinations can the AOGV be used?
We focus on the ASME class 150 & 300 in sizes from 1” to 24” but have tools that can handle sizes up to 36” ASME and up to class 2500. Please see our tool fleet at izomax.com for available off-the-shelf sizes and class combinations. Our tool fleet is continually expanding, so contact us if you don’t see the size or class you require.
How much clearance does the AOGV need either side of the flange to be installed?
As a rule of thumb, for pipes from 1”to 4” the AOGV needs 2” of clearance and from 5” and upwards a 1/2 pipe diameter is needed. The distance required is measured from the bolts and nut side of the flange.
How does the AOGV seal the full circumference of the flange and bolt holes?
The seal is pre-energised, acts as a plug, and seals directly from the circumference surface all the way inside the AOGV. The bolt holes are also plugged with mechanical plugs bolted to the AOGV kit. The seal is typically an elastomer to make sure uneven surfaces can be sealed properly
Can the AOGV be fitted on the flange of a 3-piece valve?
The AOGV can be fitted on most valve types and nozzles including 3 piece valves.
Does the pipe have to handle the weight of the AOGV?
For some of the smaller sized AOGV’s the pipe can easily handle the weight, but to mitigate any stresses, common practice is it to suspend the weight of the AOGV in chain hoists attached to a superstructure or scaffolding above the AOGV.
What about the condition of my flange?
When the Izomax team set up the AOGV on-site, we remove your old gasket at the beginning of the operation and replace it with a new gasket at the end. So far, every operation has been successfully executed with a new gasket installed and system successfully recommissioned and sealed.
How are the flanges split after the AOGV has been installed?
Either the system pressure is used for splitting the flanges or the pipe is gently moved physically e.g. with chain hoists to pull them apart. The stress tolerances are calculated for the displacements, and we analyze which location is most suitable for minimised displacements. The movement itself is carefully controlled and monitored by gradually releasing the compression exerted from the integrity clamps.